240 Produktvarianten im Takt reinigen
Unterschiedliche Produkte und Losgrößen reinigen
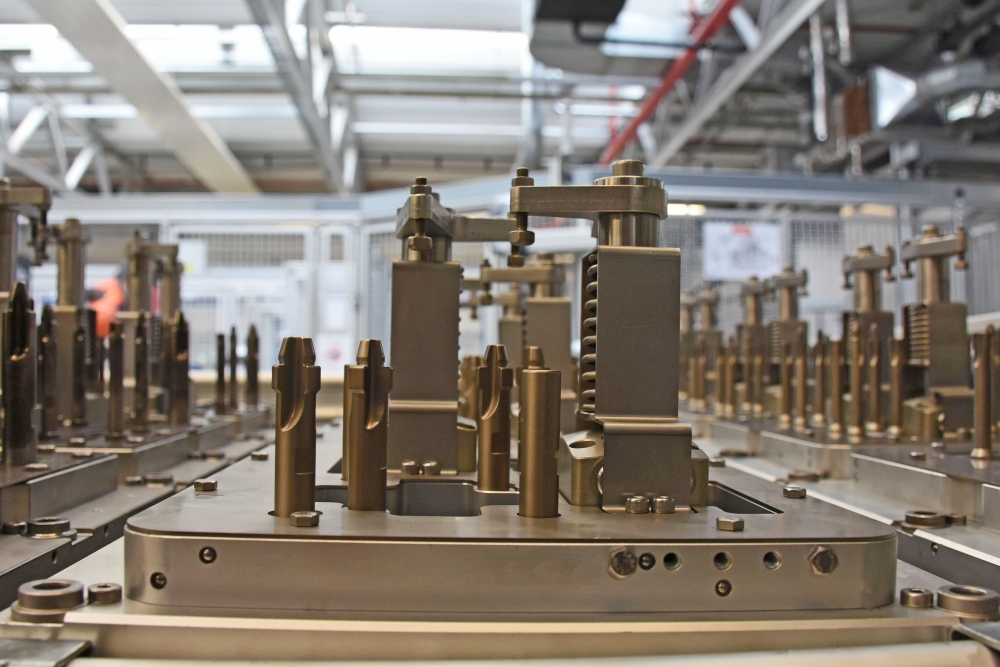
Ein Hersteller von Antriebs- und Steuerungstechnik integriert in seine Produktionsstraße eine Reinigungsanlage, die rund zehn verschiedene Bauteilfamilien automatisiert und im Fertigungstakt reinigt. Die gezielte Einzelteilreinigung der rund 240 sehr unterschiedlichen Werkstücke gelingt mit Hilfe eines ausgeklügelten Zuführsystems.
Im Zuge einer Umstrukturierung der Produktion entstand im Bereich Industriehydraulik bei der Bosch Rexroth AG eine neue verkettete Fertigungslinie. Der international tätige Anbieter von Antriebs- und Steuerungstechnik sorgt mit seinen Produkten für effiziente, leistungsstarke und sichere Bewegung in Maschinen und Anlagen jeder Art und Größenordnung. Das im bayerischen Lohr ansässige Unternehmen bündelt Praxiserfahrung und Know-how in den Marktsegmenten mobile Anwendungen, Anlagenbau und Engineering sowie Fabrikautomation. Das Angebot dafür umfasst Mobil- und Industriehydraulik, elektrische Antriebs- und Steuerungstechnik, Getriebetechnik sowie Linear- und Montagetechnik einschließlich Software und Schnittstellen für vollständig vernetzbare Anwendungen.
Der am Firmensitz angesiedelte Bereich Industriehydraulik konzentriert sich nach einer Umstrukturierung der Produktion auf technisch anspruchsvolle, komplexe Produkte, die in Losgrößen von eins bis zirka 5.000 Stück hergestellt werden. Die im Vergleich zur klassischen Serienfertigung mit Losgrößen ab 100.000 Teilen geringen Stückzahlen erforderten eine Anpassung der Fertigungskapazitäten. „Wir haben daher eine verkettete Fertigungslinie mit sieben Bearbeitungsmaschinen aufgebaut. Sie ermöglicht die vollautomatisierte Feinbearbeitung von Komponenten aus zehn Bauteilfamilien mit rund 240 Materialnummern und Stückgewichten von einem bis zwölf Kilogramm“, konkretisiert Erik Müller, der als Gesamtprojektleiter für die Umsetzung der neuen Fertigungslinie bei Bosch Rexroth verantwortlich zeichnet.


Verkettete Fertigungslinie
Die Schnittstelle zur jeweiligen Maschine bilden innerhalb dieses Produktionssystems prozessspezifisch ausgelegte Werkstückträger. Das Werkstückhandling, also das Aufspannen und Abnehmen der Teile, erfolgt durch Roboter. Um Rückstände aus vorhergehenden Bearbeitungsprozessen zu entfernen, ist in die Feinbearbeitungslinie eine Reinigungsanlage integriert.
„In der Vergangenheit wurden die Werkstücke verschiedener Bauteilfamilien in separaten Anlagen gereinigt. Durch die Zusammenführung war es wichtig, dass die neue Reinigungsanlage für die sehr große Werkstückvielfalt und die unterschiedlichen Losgrößen einsetzbar ist sowie eine einfache und schnelle Erstellung teilespezifischer Reinigungsprogramme ermöglicht. Darüber hinaus müssen die vorgegebenen produktindividuellen, partikulären Sauberkeitsspezifikationen sowie eine Oberflächenspannung von größer 38 Millinewton/Meter innerhalb der vorgegebenen Taktzeiten von 16 bis 55 Sekunden erzielt werden“, beschreibt Eva Nowak, Projektleiterin Reinigungstechnik bei Bosch Rexroth, einige Anforderungen bei der Auswahl der neuen Reinigungsanlage.
Entschieden hat sich das Projektteam für die EcoCvelox von Ecoclean, die sich zu diesem Zeitpunkt noch in der Entwicklung befand. Vorausgegangen waren Gespräche mit mehreren Herstellern von Reinigungsanlagen.

Großes Bauteilspektrum
Ausschlaggebend bei der Entscheidung für die EcoCvelox war einerseits die auf Standardmodulen für das gezielte Hochdruckentgraten, Reinigen und Trocknen basierende Bauweise. Die Anlage kann dadurch bei veränderten Durchsatzanforderungen problemlos erweitert werden. Andererseits lässt sich durch die Zuführung der Teile auf unterschiedlichen Werkstückträgern das breite Bauteilspektrum flexibel abbilden.
Der Transport der Werkstückträger zwischen den Bearbeitungseinheiten erfolgt durch ein serienmäßig integriertes, hochdynamisches Linearsystem mit verschleißfreiem Motor. „Die Alternative dazu wäre eine Anlage gewesen, bei der Roboter die Teile greifen und an den verschiedenen Lanzen vorbeifahren. Um das in unseren kurzen Taktzeiten zu realisieren, wären sehr viele Roboter erforderlich gewesen, die die gleiche Aufgabe erledigen. Hinzu kommt, dass die feuchte Atmosphäre in einer Reinigungsanlage einen erhöhten Wartungsaufwand an den Robotern verursacht, der die Anlagenverfügbarkeit verringert“, ergänzt Erik Müller. Punkten konnte die EcoCvelox außerdem durch ihre serienmäßig integrierte CAD-/CAM-Schnittstelle wie sie auch bei Werkzeugmaschinen zu finden ist.

Bedarfsgerechte Prozesse
In die Fertigungslinie bei Bosch Rexroth ist eine aus drei Modulen – gezieltes Hochdruckentgraten, Reinigung und Trocknung – bestehende Anlage von Ecoclean integriert. Aufgrund der kurzen Taktzeiten verfügt die Hochdruckeinheit über eine optionale zweite Y-Achse für das Teilehandling. Das Be- und Entladen kann dadurch parallel zur Bearbeitung durchgeführt werden. Ausgestattet ist das Modul darüber hinaus mit einem für vier Werkzeuge ausgelegten Hochdruckrevolver, der momentan mit zwei an die Applikation angepassten Tools bestückt ist. Bei der Reinigungs- und Trocknungseinheit trägt jeweils eine zweite Kammer ebenfalls zu sehr kurzen Taktzeiten durch paralleles Be- und Entladen bei.
Für die Reinigung werden die aus geschmiedetem Stahl sowie Grauguss hergestellten Teile im Serienbetrieb mittels Roboter auf die Werkstückträger gespannt. Die Möglichkeit einer manuellen Bestückung besteht ebenfalls. Insgesamt sind für die rund 240 Bauteilvarianten nur neun verschiedene Werkstückträger im Einsatz. Sie werden je nach zu reinigenden Werkstücken mit einem bis zu vier Teilen bestückt.

Ein Werkstückträger – viele Teile
„Es war eine große Denkleistung, so viele Teile wie möglich aus verschiedenen Familien auf einen Werkstückträger zu bringen. Die Konstruktionsabteilungen von Ecoclean und Bosch Rexroth haben dafür sehr gut zusammengearbeitet“, merkt Eva Nowak an. Der Reinigung vorgeschaltet ist ein Hon- oder Entgratprozess. Da bei Letzterem auch Außenkanten zu bearbeiten sind, wird das Hochdruckentgratmodul derzeit in erster Linie für die gezielte Reinigung der Bohrungen mit den Lanzen des Revolvers genutzt. Dabei wird mit einem werkstückspezifischen Druck von bis zu 600 bar gearbeitet.
„Die Entfernung innenliegender Grate mit der EcoCvelox ist ein Technologiesprung, den wir uns momentan noch vorbehalten. Sobald die neue Feinbearbeitungslinie komplett verkettet ist und reibungslos läuft, werden wir mit der Prozessoptimierung beginnen, zu der auch die Entgratung zählt“, berichtet Erik Müller. Für die Bauteilreinigung im anschließenden Reinigungsmodul stehen die Prozesse Injektionsflutwaschen, Spritzreinigung und gezieltes Spülen zur Verfügung, die kombiniert werden können. In der Trocknungseinheit erfolgt zunächst ein Hochgeschwindigkeitsabblasen, dem sich eine Vakuumtrocknung anschließt.
Nach der Reinigung durchlaufen die Teile entsprechend den Anforderungen verschiedene Sauberkeitskontrollen. „Die Anlage muss für die Produkte jeder Bauteilfamilie freigefahren werden. Dafür führen wir Kontrollen zur partikulären Sauberkeit entsprechend VDA 19 sowie zur Oberflächenspannung durch. Weitere wesentliche Kriterien sind unter anderem die Lackhaftfestigkeit und der Korrosionsschutz“, bemerkt Eva Nowak.
Nicht nur beim Optimieren der Prozessparameter, sondern bereits bei der Erstellung der bisher eingesetzten 35 teilespezifischen Entgrat-/Reinigungsprogramme erweist sich die CAD-/CAM-Schnittstelle als signifikante Vereinfachung. Denn sie ermöglicht, Daten aus der Bauteilkonstruktion für die Programmierung zu übernehmen, die offline erfolgt. Das Programm wird anschließend einfach in die Anlagensteuerung eingespielt. Dadurch lässt sich die Reinigung/Entgratung zukünftiger Produktfamilien und neuer Bauteile ebenso effektiv und wirtschaftlich integrieren, wie die Bearbeitung von Teilen in Losgröße 1.

Pilotkunde für Reinigung kleiner Losgrößen im Takt
„Die Schulungen für die Programmierung mussten aufgrund der Corona-Pandemie online stattfinden. Die Mitarbeiter von Ecoclean haben das gut gemacht, denn unsere Kollegen sagen heute, dass die Programmierung schnell und einfach durchführbar ist und Spaß macht“, ergänzt Eva Nowak. „Es ist sicher nicht üblich, dass ein Unternehmen wie Bosch Rexroth Pilotkunde für eine völlig neu entwickelte Anlage wird und damit bewährte Pfade verlässt. Aber das Konzept dieser Reinigungslösung hat uns von Anfang an überzeugt und bietet uns auch Reserven für zukünftige Entwicklungen“, merkt Erik Müller abschließend an.
Ecoclean GmbH
www.ecoclean-group.net
Bosch Rexroth AG
www.boschrexroth.com